物流改善事例:破損事故撲滅
新規案件立ち上げで物流品質事故が増加
庫内作業ルールの明確化で発生件数を削減
当社の関西エリアにある物流センターでは、お客様からお預かりしている商品の物流品質事故の発生件数が増加傾向にありました。具体的には、フォークリフト操作ミスや積み付けミスによる商品の破損や、数量やアイテム、日付の間違いなどのピッキングミスが発生し、それに伴うコスト負担増を余儀なくされていました。
同センターでは、こうした事故が発生する要因として、2つの新規案件が同時期にスタートしたことで物量の把握や庫内ロケーションの設定がうまく機能していないためであると分析。その改善策として、庫内作業ルールの明確化に取り組むことにしました。
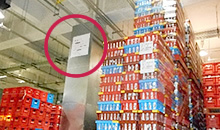
まず、ラック間の通路スペースに直置きしていたパレット荷物を、他の格納場所に移動させました。これは、フォークリフトの通行の妨げをなくすことで、フォークリフトでの作業時に発生していた製品との接触事故を防ぐのが目的です。さらに、センターの天井部分に設置している冷凍機の近くには、フォークリフトやパレット荷物が冷凍機に触れないよう注意喚起する目印を施しました。
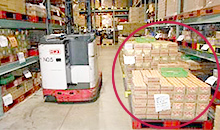
このほかにも、ピッキングに使用する台車に積載量の上限を設定したり、作業員に段積みの制限を伝える表記を用意するなど、破損事故防止のための具体策を実施いたしました。
ピッキング作業については、日付の逆転出荷の防止に取り組みました。先入れ先出し等を徹底するため、同じアイテムの商品でも製造ロットごとに、在庫量と格納場所を明確にし、その情報を、朝礼などで作業員に伝達・共有。誤出荷を発生させないようにしました。
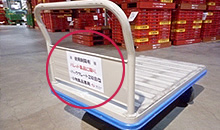
段積み制限を掲示!
こうした一連の改善活動によって、同センターでは破損や誤出荷などの事故の発生件数はもちろん、負担コスト(事故費)も大幅に削減することに成功しました。
-
食品メーカーA社様
〔受注システム〕 -
食品メーカーB社様
〔受注センター〕 -
食品メーカーC社様
〔WMS〕 -
乳製品メーカーD社様
〔食品工場内物流〕 -
(株)KOMPEITO様
〔センター運営〕 -
食品卸E社様
〔センター納品〕 -
冷凍食品メーカーF社様
〔モーダルシフト〕 -
飲料メーカーG社様
〔冷蔵共同配送〕 -
大手CVSチェーンH社様
〔センター運営〕 -
食品メーカーJ社様
〔共配センター〕 -
大手CVSチェーンK社様
〔センター運営〕 -
乳製品メーカーL社様
〔食品工場内物流〕 -
大手コンビニエンスストアM社様
〔冷蔵ルート輸送〕 -
外食チェーンN社様
〔冷凍・冷蔵・常温一括輸送〕 -
乳製品メーカーO社様
〔配車センター〕 -
大手量販店P社様
〔ネットスーパー〕 - 破損事故撲滅
- 誤出荷対策
-
北摂センター
〔センター運営事例〕